Machinery Vibration Analysis Data
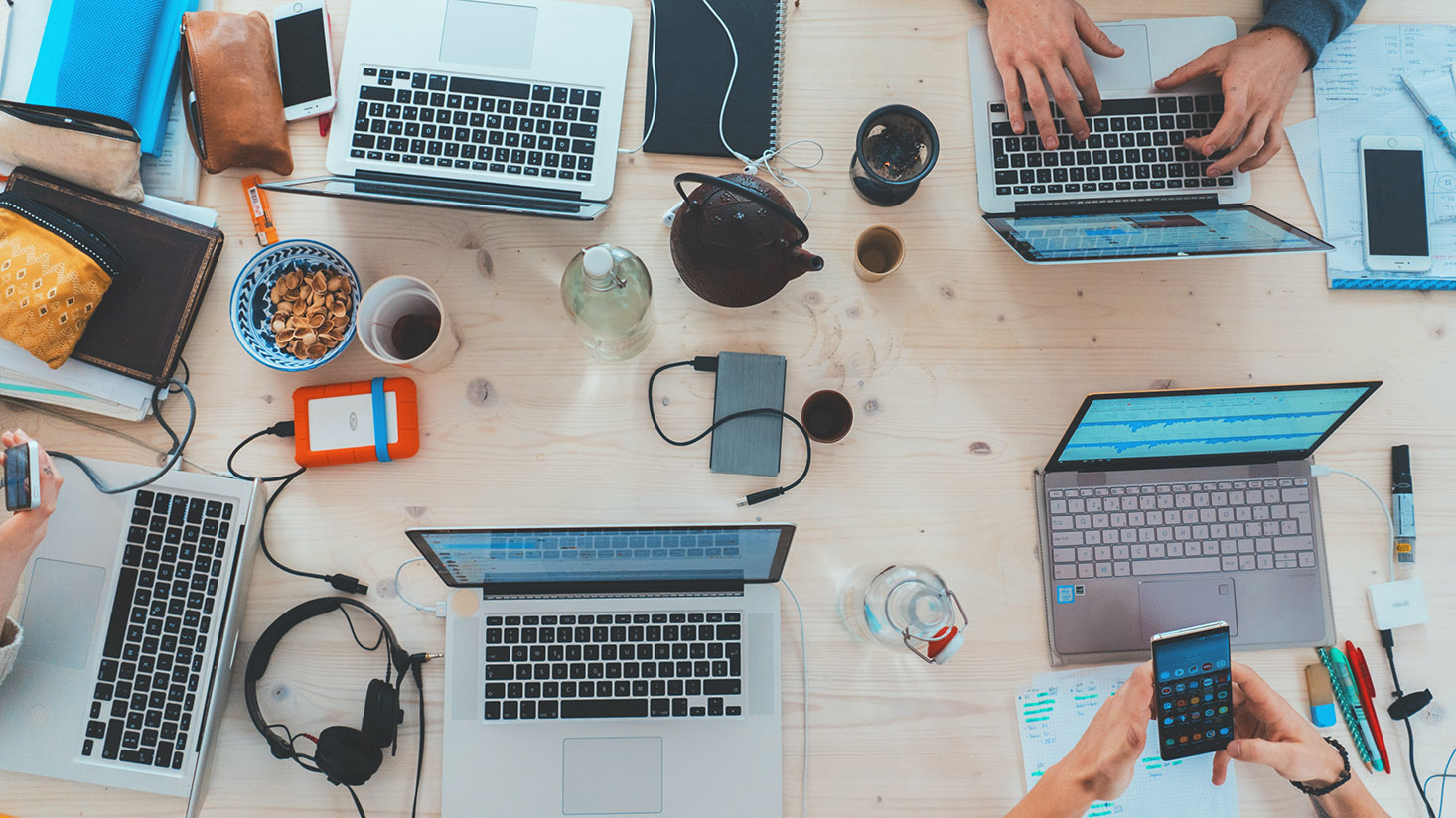
Introduction
In the realm of industrial maintenance and machinery health monitoring, understanding the intricacies of rotating machinery has always been a challenge. Historically, the ability to predict failures in rotating machinery such as turbines, gearboxes, and rotors was limited by the technology and methods available. Before the digital age, maintenance was often reactive rather than proactive, relying on visual inspections, manual measurements, and the experience of engineers. These methods, while valuable, were time-consuming and often resulted in downtime that could have been avoided.
The advent of sensors, the internet, and connected devices has revolutionized how we approach machinery maintenance. Previously, data was scarce and often not timely, leaving businesses in the dark about the health of their machinery until a failure occurred. The proliferation of software and the move towards digitizing every aspect of industrial operations have made it possible to collect and analyze data in real time, transforming maintenance strategies from reactive to predictive.
The importance of data in understanding and predicting failures in rotating machinery cannot be overstated. With the right data, businesses can monitor the condition of their machinery continuously, identify potential issues before they lead to failure, and schedule maintenance more effectively. This shift towards data-driven maintenance strategies has the potential to save businesses significant amounts of time and money, while also improving safety and reliability.
However, collecting and analyzing the right data is not without its challenges. The types of data relevant to machinery health monitoring are vast and varied, and understanding which data types are most useful can be daunting. This article will explore several key categories of data that are critical to understanding and predicting failures in rotating machinery. By examining the history, examples, and applications of these data types, we aim to provide insights into how they can be used to improve machinery maintenance and reliability.
Research Data for Vibration Analysis
History and Evolution
The study of machinery vibration and its impact on machinery health has a long history. Initially, vibration analysis was conducted manually, with engineers relying on their senses and simple tools to detect anomalies. The development of electronic sensors and data acquisition systems marked a significant advancement, enabling more precise and continuous monitoring of machinery vibration.
Advancements in sensor technology and data analysis software have further enhanced our ability to collect and interpret vibration data. Today, sophisticated sensors can capture high-frequency, multi-axial vibration data, providing a detailed picture of machinery health. The advent of machine learning and artificial intelligence has also opened new possibilities for analyzing this data, allowing for more accurate predictions of machinery failure.
Examples of Vibration Data
- Bearings vibration analysis fault detection: Datasets used for identifying faults in machinery bearings through vibration analysis.
- Vibration Measurements on Rotating Shafts: Data recorded on rotating drive trains to detect unbalances and other anomalies.
- Condition-monitoring techniques: Various techniques such as acoustic emission, vibration, and lubricant monitoring used to assess machinery health.
Applications and Insights
Vibration data is invaluable for predicting failures in rotating machinery. By analyzing patterns and anomalies in vibration data, maintenance teams can identify issues such as unbalance, misalignment, bearing failures, and gear defects. This data can be used to:
- Prevent unplanned downtime: By detecting issues early, businesses can schedule maintenance and repairs before failures occur.
- Improve machinery lifespan: Regular monitoring and maintenance based on vibration data can extend the life of machinery.
- Enhance safety: Early detection of potential failures can prevent accidents and improve workplace safety.
The use of vibration analysis data is not limited to any specific industry. It is widely used in sectors such as manufacturing, energy, aerospace, and automotive, where rotating machinery plays a critical role.
Conclusion
The importance of data in understanding and predicting failures in rotating machinery cannot be overstated. With advancements in sensor technology and data analysis, businesses now have the tools to monitor machinery health in real time, identify potential issues before they lead to failure, and schedule maintenance more effectively. This shift towards data-driven maintenance strategies has the potential to save businesses significant amounts of time and money, while also improving safety and reliability.
As organizations become more data-driven, the discovery and utilization of relevant data types will be critical to improving machinery maintenance and reliability. The future may see the development of new types of data that can provide even deeper insights into machinery health, further enhancing our ability to predict and prevent failures.
In conclusion, the role of data in machinery maintenance is evolving rapidly, and businesses that embrace this change will be better positioned to improve their operations and competitiveness. The journey towards predictive maintenance is complex, but with the right data and analysis tools, it is a journey that can lead to significant rewards.
Appendix
Industries and roles that can benefit from machinery vibration analysis data include:
- Manufacturing: Maintenance engineers and operations managers can use vibration data to optimize production schedules and reduce downtime.
- Energy: In the energy sector, vibration data can help monitor the health of turbines and generators, ensuring reliable power generation.
- Aerospace: Aircraft maintenance teams can use vibration data to monitor engine health and prevent in-flight failures.
- Automotive: Automotive manufacturers can use vibration analysis to ensure the reliability of engines and drivetrains in vehicles.
The future of machinery maintenance is likely to be shaped by advances in AI and machine learning, which can unlock the value hidden in decades-old documents or modern government filings. As these technologies continue to evolve, they will enable more sophisticated analysis of vibration data, leading to even more effective predictive maintenance strategies.